Drilling is a crucial part of many DIY projects and professional construction jobs. Having the right tools for the job can make all the difference in the project’s outcome. When it comes to drilling, various types of drill bits are available on the market. Two of the most common types are self-centering drill bits and regular drill bits. Understanding the differences between these two types of drill bits is essential to determine which is best suited for a particular project.
This article will explore the working mechanism, advantages, and disadvantages of self-centering and regular drill bits. We will also discuss when to use each type of drill bit and how to choose the right one for a specific project. We will also compare these two types of drill bits based on various factors and help you decide which is better for your drilling needs.

What Are Self-Centering Drill Bits?
If you are into woodworking or metalworking, you would know the importance of having the right tools for the job. One such tool that is essential for these activities is a drill bit. There are various types of drill bits available in the market. However, in this article, we will focus on self-centering drill bits.
Definition of Self-Centering Drill Bits
A self-centering drill bit is a type of drill bit that has a spring-loaded guide attached to the tip. This guide helps the bit stay in the hole’s center while drilling. Self-centering drill bits come in various sizes and can be used for drilling holes in wood, metal, and plastic.
Types of Self-Centering Drill Bits
There are mainly two self-centering drill bits: brad point bits and Vix bits.
Brad Point Bits
Brad-point bits, also known as doweling bits, are designed with a pointed tip surrounded by two sharp edges. These bits are used for drilling holes in wood and are excellent for creating precise and clean holes. The pointed tip helps to guide the bit, preventing it from wandering and creating off-center holes.
Vix Bits
Vix bits are designed with a spring-loaded guide that ensures the bit stays in the center of the hole while drilling. These bits are primarily used for drilling holes in metal and can drill through sheet metal, aluminum, and brass. The spring-loaded guide helps to prevent the bit from slipping or wandering, ensuring precise and accurate holes.
Advantages of Using Self-Centering Drill Bits
Using self-centering drill bits has several advantages. Some of them are:
Accurate and Precise Holes
Self-centering drill bits are designed to stay in the center of the hole while drilling. This feature ensures that the holes are accurate and precise, which is essential when working with wood or metal.
Reduced Risk of Bit Wandering
Bit wandering occurs when the drill bit moves off-center while drilling, which can cause damage to the material being drilled. Self-centering drill bits have a guide that helps to keep the bit in the center of the hole, reducing the risk of bit wandering.
Faster and Easier Drilling
Self-centering drill bits are designed to drill faster and easier than traditional ones. With the guide helping to keep the bit in the center of the hole, there is less resistance, which makes drilling faster and less strenuous.
Versatility
Self-centering drill bits can be used to drill various materials such as wood, metal, and plastic, making them versatile tools in any workshop or garage.
Cost-Effective
Although self-centering drill bits may be slightly more expensive than traditional ones, their accuracy and precision can help save time and money in the long run.
In conclusion, self-centering drill bits are helpful for anyone working with wood, metal, or plastic. They offer accuracy, precision, and versatility, making them an essential tool in any workshop or garage.

What Are Regular Drill Bits?
Drill bits are essential tools in woodworking, metalworking, and construction. Various types of drill bits are available in the market, each with its unique purpose. In this article, we will focus on regular drill bits.
Definition of Regular Drill Bits
Regular drill bits are the most commonly used drill bits in the market. These bits are designed with a spiral-shaped flute that helps to remove debris from the hole while drilling. Regular drill bits come in various sizes and can be used to drill holes in wood, metal, plastic, and other materials.
Types of Regular Drill Bits
There are mainly two types of regular drill bits: twist drill bits and spade bits.
Twist Drill Bits
Twist drill bits are the most common type of regular drill bits. These bits are designed with a twisted flute that helps to remove debris from the hole while drilling. Twist drill bits can be used to drill various materials such as wood, metal, and plastic.
Spade Bits
Spade bits, also known as paddle bits, are designed with a flat, paddle-shaped tip that helps quickly create large holes. These bits are commonly used to drill holes in wood and can create holes with diameters up to two inches.
Advantages of Using Regular Drill Bits
Using regular drill bits has several advantages. Some of them are:
Versatility
Regular drill bits are versatile and can be used to drill holes in various materials such as wood, metal, and plastic.
Cost-Effective
Regular drill bits are cost-effective and readily available in the market.
Speed
Regular drill bits are designed to drill quickly, making them ideal for large-scale projects.
Ease of Use
Regular drill bits are easy to use, making them suitable for novice and experienced users.
In conclusion, regular drill bits are a versatile and cost-effective tool for anyone working with wood, metal, or plastic. They offer speed and ease of use and can be used for various projects, making them an essential tool in any workshop or garage.
How Do Self-Centering Drill Bits Work?
Self-centering drill bits are innovative tools designed to make drilling easier, faster, and more accurate. These bits are becoming increasingly popular among woodworkers, metalworkers, and DIY enthusiasts. Here will discuss the working mechanism of self-centering drill bits and compare them with regular drill bits.
Explanation of the Working Mechanism of Self-Centering Drill Bits
Self-centering drill bits are designed with a spring-loaded guide that helps to keep the bit centered and aligned with the material being drilled. The guide is located at the bit’s tip and consists of two or more jaws that retract as the bit enters the material. Once the bit is in place, the jaws expand and hold the bit in the center of the hole, ensuring accurate drilling.
Self-centering drill bits are handy when drilling pilot holes for screws, hinges, or dowels. The guide ensures that the pilot hole is precisely centered, making it easier to insert the fastener and ensuring a secure and tight fit.
Comparison of the Working Mechanism of Self-Centering Drill Bits with Regular Drill Bits
Regular drill bits do not have a guide and rely on the user to keep the bit centered and aligned with the material being drilled. This can be challenging, especially when drilling smaller holes or using hand-held drills. Regular drill bits can easily wander off-center, resulting in inaccurate holes.
On the other hand, self-centering drill bits eliminate the need for the user to keep the bit centered and aligned. The guide ensures the bit stays centered, resulting in precise and accurate holes every time. This makes them ideal for beginners, DIY enthusiasts, and professionals who want to achieve accurate results quickly and easily.
In conclusion, self-centering drill bits are innovative tools that make drilling faster, easier, and more accurate. They use a spring-loaded guide to keep the bit centered and aligned with the drilled material. Self-centering drill bits offer better accuracy and precision than regular drill bits, making them an ideal choice for anyone looking to achieve accurate results quickly and easily.
How Do Regular Drill Bits Work?
Regular drill bits are among the most commonly used tools in woodworking, metalworking, and DIY projects. They are designed to cut through various materials, including wood, metal, plastic, and masonry. Here, we will discuss the working mechanism of regular drill bits and compare them with self-centering drill bits.
Explanation of the Working Mechanism of Regular Drill Bits
Regular drill bits are made of high-speed steel, cobalt, or carbide and come in various sizes and shapes. The bit has a spiral-shaped flute that helps to remove the material as the bit rotates. The tip of the bit is designed to cut into the material and create a hole.
When drilling with a regular drill bit, the user must keep the bit centered and aligned with the drilled material. This can be challenging, especially when drilling smaller holes or using hand-held drills. If the bit wanders off-center, the hole will be inaccurate and unsuitable for its intended use.
Comparison of the Working Mechanism of Regular Drill Bits with Self-Centering Drill Bits
Regular drill bits rely on the user to keep the bit centered and aligned with the drilled material. This can be challenging, especially for beginners or when drilling smaller holes. Self-centering drill bits eliminate the need for the user to keep the bit centered and aligned by using a spring-loaded guide that keeps the bit in the center of the hole.
Regular drill bits are less accurate than self-centering drill bits and may require more skill and experience. However, regular drill bits are more versatile. They can drill a broader range of materials and hole sizes.
In summary, regular drill bits use a spiral-shaped flute to remove the material as the bit rotates. The user must keep the bit centered and aligned with the drilled material. Regular drill bits are less accurate but more versatile than self-centering drill bits.
Pros and Cons of Self-Centering Drill Bits
Self-centering drill bits have become increasingly popular in recent years due to their ease of use and accuracy. These bits are designed to eliminate the need for the user to keep the bit centered and aligned with the material being drilled. This article will discuss the advantages and disadvantages of using self-centering drill bits and compare them with regular drill bits.
Advantages of Using Self-Centering Drill Bits
- Increased accuracy: Self-centering drill bits are more accurate than regular drill bits because they eliminate the need for the user to keep the bit centered and aligned with the material being drilled.
- Faster drilling: With self-centering drill bits, the user can drill holes more quickly because they do not need to adjust the bit’s position constantly.
- Reduced risk of damage: Self-centering drill bits reduce the risk of damaging the drilled material because they are less likely to wander off-center.
- Suitable for beginners: Self-centering drill bits are easy to use and require less skill and experience than regular drill bits, making them ideal for beginners.
Disadvantages of Using Self-Centering Drill Bits
- Limited sizes: Self-centering drill bits are available in a limited range of sizes, making them less versatile than regular drill bits.
- Higher cost: Self-centering drill bits are more expensive than regular drill bits.
- Reduced control: Self-centering drill bits provide less control than regular drill bits because the user needs to adjust the bit’s position.
Comparison of Self-Centering Drill Bits with Regular Drill Bits
Compared to regular drill bits, self-centering drill bits offer several advantages, such as increased accuracy, faster drilling, and reduced risk of damage. However, they also have disadvantages, such as a limited range of sizes, higher cost, and reduced control.
Regular drill bits are more versatile and can be used to drill a broader range of materials and hole sizes. They require more skill and experience to use effectively but offer more control over the drilling process.
In summary, self-centering drill bits offer several advantages over regular drill bits, such as increased accuracy and faster drilling. However, they also have disadvantages, such as a limited range of sizes and reduced control. When choosing between self-centering drill bits and regular drill bits, it is essential to consider the project’s specific needs.
Pros and Cons of Regular Drill Bits
Regular drill bits have been a staple tool in every toolbox for decades. They come in different sizes and shapes, but all work on the same principle. This section will discuss the advantages and disadvantages of using regular drill bits and compare them with self-centering drill bits.
Advantages of using regular drill bits
- Versatility: Regular drill bits can be used for various applications, including drilling through wood, metal, plastic, and other materials.
- Affordability: Regular drill bits are less expensive than self-centering drill bits, making them a more accessible option for DIY enthusiasts and homeowners.
- Availability: Regular drill bits are widely available in hardware stores and online, making them easy to purchase and replace.
Disadvantages of using regular drill bits
- Lack of accuracy: Regular drill bits require a steady hand and much practice to achieve a precise hole. They do not have a self-centering mechanism, making it easy for the bit to wander off-center.
- Risk of damage: Regular drill bits can easily damage the material if the user lacks experience.
- Time-consuming: Achieving accurate holes with regular drill bits takes time and patience. The user must mark the drilling spot accurately and drill slowly to avoid damaging the material.
Comparison of regular drill bits with self-centering drill bits
Regular drill bits are an excellent option for those on a budget and those who don’t require precise holes. However, for those who need more accurate holes or lack the necessary experience, self-centering drill bits are a better choice. Compared to regular drill bits, self-centering drill bits have the following advantages:
- Precision: Self-centering drill bits are designed to keep the bit centered and aligned, resulting in a more precise hole.
- Ease of use: Self-centering drill bits are designed to be easy to use and require less experience and skill to achieve accurate results.
- Time-saving: Self-centering drill bits are faster than regular drill bits, as they eliminate the need to mark the drilling spot and drill slowly.
Disadvantages of using self-centering drill bits
- Limited sizes: Self-centering drill bits are not available in as many sizes as regular drill bits, limiting their versatility.
- Cost: Self-centering drill bits are more expensive than regular drill bits, making them less accessible to those on a tight budget.
- Fragility: Self-centering drill bits are more fragile than regular ones and can easily break if dropped or mishandled.
In conclusion, regular drill bits are an excellent option for those on a budget and those who don’t require precise holes. Self-centering drill bits are a better choice for those who need more accurate holes or lack the necessary experience. Choosing between regular and self-centering drill bits depends on the user’s needs and budget.
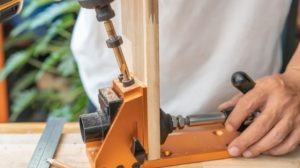
When to Use Self-Centering Drill Bits
Self-centering drill bits are the best option when drilling holes into materials that require precision and accuracy. These materials include metals, plastics, and wood. Here are some situations where self-centering drill bits are the best option:
- When drilling angled or slanted holes: Self-centering drill bits are excellent for drilling angled or slanted holes in materials. The drill bits automatically adjust to the angle of the material and create a precise and accurate hole.
- When working with thin or fragile materials: Thin or fragile materials, such as glass or acrylic, require delicate handling when drilling. Self-centering drill bits can provide a stable and centered drilling point, reducing the likelihood of material breakage or damage.
- When working with uneven or curved surfaces: Uneven or curved surfaces can make achieving a centered drilling point challenging. Self-centering drill bits adjust to the surface, creating a precise hole every time.
Materials requiring self-centering drill bits include circuit boards, metal sheets, and PVC pipes.
In summary, self-centering drill bits are ideal for precision drilling tasks where accuracy is critical and materials require delicate handling. They are handy for drilling angled or slanted holes, working with thin or fragile materials, and drilling on uneven or curved surfaces.

When to Use Regular Drill Bits
Regular drill bits are versatile tools that can be used for various drilling tasks. Here are some situations where regular drill bits are the best option:
- When drilling large holes: Regular drill bits are more efficient than self-centering drill bits when drilling large holes. They have a larger cutting surface, allowing for faster drilling and a more significant hole size.
- When working with soft materials: Soft materials such as wood or plaster do not require the precision of a self-centering drill bit. Regular drill bits are the best option for these materials as they can quickly create holes without damaging them.
- When working with low-budget projects: Regular drill bits are cheaper than self-centering drill bits, making them the better option for low-budget projects.
Materials requiring regular drill bits include wood, drywall, and soft plastics.
In summary, regular drill bits are a versatile option that can be used for various drilling tasks. They are ideal for drilling large holes, working with soft materials, and doing low-budget projects. Regular drill bits are cost-effective and widely available, making them a practical choice for many DIY and construction projects.
Self Centering Drill Bits vs. Regular Drill Bits: Which One Is Better?
When choosing the right drill bit for your project, it’s essential to consider the advantages and disadvantages of both self-centering drill bits and regular drill bits. Here’s a comparison of the two types of drill bits to help you determine which is better for your needs.
Comparison of Self Centering Drill Bits and Regular Drill Bits
Self-centering drill bits are designed to center themselves automatically on a surface, eliminating manual alignment. This feature makes them ideal for drilling accurate holes in wood, plastic, and metal materials. On the other hand, regular drill bits require manual alignment, which can be time-consuming and may result in imprecise holes.
In terms of speed, self-centering drill bits are faster and more efficient than regular drill bits. They require less force to drill through materials, which reduces the risk of breaking or dulling the bit. On the other hand, regular drill bits require more force to drill through materials, which can result in slower progress and more wear and tear on the bit.
Regarding versatility, regular drill bits are more versatile than self-centering drill bits. Regular bits come in a wide range of sizes and shapes, making them suitable for drilling various hole sizes and shapes. Self-centering drill bits, however, are limited in size and shape options.
Factors to Consider When Determining the Best Drill Bit for a Specific Project
When deciding between self-centering drill bits and regular drill bits, there are several factors to consider:
- Material: Consider the type of material you will be drilling into. Self-centering drill bits are ideal for softer wood, plastic, and thin metal sheets. Regular drill bits are better suited for drilling into more complex materials like concrete, masonry, and thicker metal sheets.
- Hole size and shape: Consider the size and shape of the hole you need to drill. Regular drill bits come in a broader range of sizes and shapes, which makes them more versatile for drilling different hole sizes and shapes. Self-centering drill bits are more limited in their size and shape options.
- Precision: Self-centering drill bits may be better if you require precise and accurate holes, as they eliminate manual alignment. Regular drill bits require manual alignment, which can result in imprecise holes.
- Speed: If you need to drill holes quickly and efficiently, self-centering drill bits are the better option as they require less force and are faster and more efficient than regular drill bits.
Final Verdict on Which One Is Better
In conclusion, the choice between self-centering and regular drill bits depends on the specific project requirements. Self-centering drill bits are ideal for softer materials and when precision is required. They are also faster and more efficient than regular drill bits. Regular drill bits, on the other hand, are more versatile and better suited for drilling into more rigid materials.
Both drill bits in your toolkit are recommended, as they each have unique advantages and disadvantages. This will ensure that you have the right tool for the job, no matter what project you’re working on.
Conclusion
In conclusion, drill bits are an essential tool in any drilling project. Whether for personal use or professional applications, selecting the correct type of drill bit can significantly impact the project’s outcome. This article provided an in-depth look at self-centering and regular drill bits, including their definitions, types, advantages, and disadvantages.
Self-centering drill bits offer many benefits, including improved accuracy, reduced slipping, and quicker drilling times. On the other hand, regular drill bits are more versatile and are suitable for a broader range of materials. Ultimately, the choice between self-centering and regular drill bits will depend on the specific project and the drilled materials.
When choosing a drill bit, it’s essential to consider factors such as the material being drilled, the type of drill being used, the size and shape of the hole, and the required accuracy. It’s also essential to ensure the drill bit is compatible with the drill being used.
In conclusion, both self-centering and regular drill bits have advantages and disadvantages. Choosing the best drill bit for a specific project requires careful consideration of the materials, the drilling needs, and the desired outcome. Any drilling project can be completed accurately and efficiently with the right drill bit and proper technique.
You may also like these posts!