The article provides a comprehensive guide to cordless drills and their functionality. It explores the different types of cordless drills and screwdrivers available. It helps readers choose the right tool for their needs. The article highlights how to use cordless drill as screwdriver and the benefits of using a cordless drill as a screwdriver and provides techniques for efficient usage. It also emphasizes safety precautions to ensure injury-free operation. By the end of the article, readers will have a solid understanding of cordless drills and be able to make informed decisions when using them.
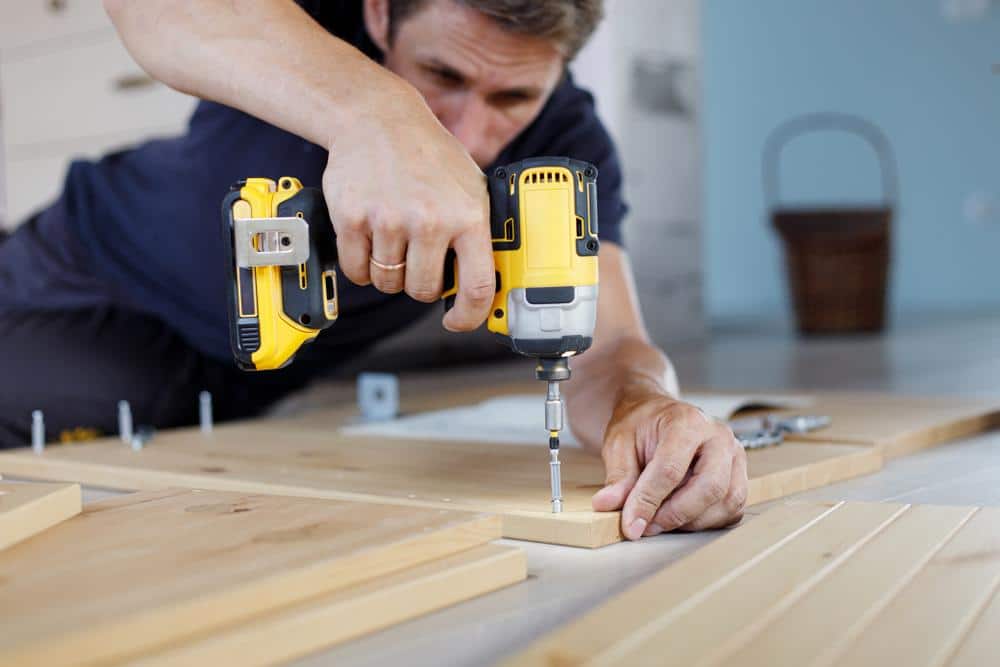
1. Introduction
Cordless drills are versatile power tools that have revolutionized how we handle DIY projects, woodworking, and various other tasks. These tools provide convenience, mobility, and freedom from the limitations of cords. This section delves into what cordless drills are and how they function.
I. What is a Cordless Drill?
A cordless drill is a portable power tool designed to drill holes and drive screws efficiently. Unlike traditional corded drills, cordless drills operate on rechargeable batteries, allowing users to move around without being tethered to a power outlet. They come in various sizes and configurations, offering different levels of power and performance.
II. How Does a Cordless Drill Work?
Cordless drills consist of a motor, a gearbox, a clutch, a chuck, and a battery. When the trigger is pressed, it activates the motor, which drives the gearbox. The gearbox transfers the power to the chuck, where different drill bits or screwdriver bits can be attached. The clutch allows users to control the torque applied, preventing overdriving or stripping of screws. The battery provides the necessary power to run the drill and can be recharged.
2. Different Types of Cordless Drills and Screwdrivers
When it comes to cordless drills and screwdrivers, there are several options available in the market. Understanding the different types can help you choose the one that best suits your needs. Some common types include:
I. Cordless Drill/Driver
This type of drill is designed for drilling and screw-driving applications. It offers versatility and is suitable for a wide range of tasks.
II. Impact Driver
An impact driver is specifically designed for driving screws and fasteners. It delivers high torque and is ideal for heavy-duty applications.
III. Hammer Drill
Hammer drills can drill into masonry and concrete surfaces. They combine rotational drilling with a hammering action to provide extra power.
IV. Screwdriver
Cordless screwdrivers are compact and lightweight tools primarily used for driving screws. They are ideal for tasks that require precision and control.

3. Choosing the Right Cordless Drill
When selecting a cordless screwdriver or drill, there are a few factors to consider:
I. Power and Voltage
The drill’s voltage rating determines its power. Higher voltage drills generally offer more power, making them suitable for heavy-duty applications.
II. Battery Life and Capacity
Consider the battery life and capacity of the drill. Longer battery life allows for extended use without recharging, while higher-capacity batteries provide more power.
III. Speed and Torque Settings
Look for a drill with adjustable speed and torque settings. This will give you greater control over the tool and enable you to adapt to different tasks.
IV. Ergonomics and Comfort
Consider the design and ergonomics of the drill. A comfortable grip and well-balanced weight distribution can reduce fatigue during prolonged use.
V. Accessories and Features
Check for additional features such as LED lights, built-in levels, and magnetic bit holders, as these can enhance the functionality and convenience of the drill.
4. Benefits of Using a Cordless Drill as a Screwdriver
Using a cordless drill as a screwdriver offers several benefits:
I. Versatility
Cordless drills are multi-purpose tools that handle drilling and screw-driving tasks. This versatility eliminates the need for separate tools, saving time and money.
II. Mobility
Cordless drills provide freedom of movement as power cords do not restrict them. You can easily maneuver the drill in tight spaces or work areas without worrying about the cord getting tangled or limiting your reach.
III. Convenience
With a cordless drill, you can work anywhere, whether inside your house or outside in the yard. You’re not limited to areas with power outlets, allowing for greater convenience and ease of use.
IV. Time-saving
Cordless drills are generally more powerful than manual screwdrivers, allowing you to drive screws more quickly and efficiently. This can significantly speed up your projects and save you valuable time.
V. Increased Power and Control
Cordless drills offer adjustable speed and torque settings, enabling you to customize the driving force according to the type of screw and material you’re working with. This provides better control and reduces the risk of damaging the screw or the work surface.
VI. Accessibility
Using a cordless drill as a screwdriver makes accessing hard-to-reach areas or overhead installations easier. The compact size and lightweight design of cordless drills allow for greater accessibility and maneuverability.
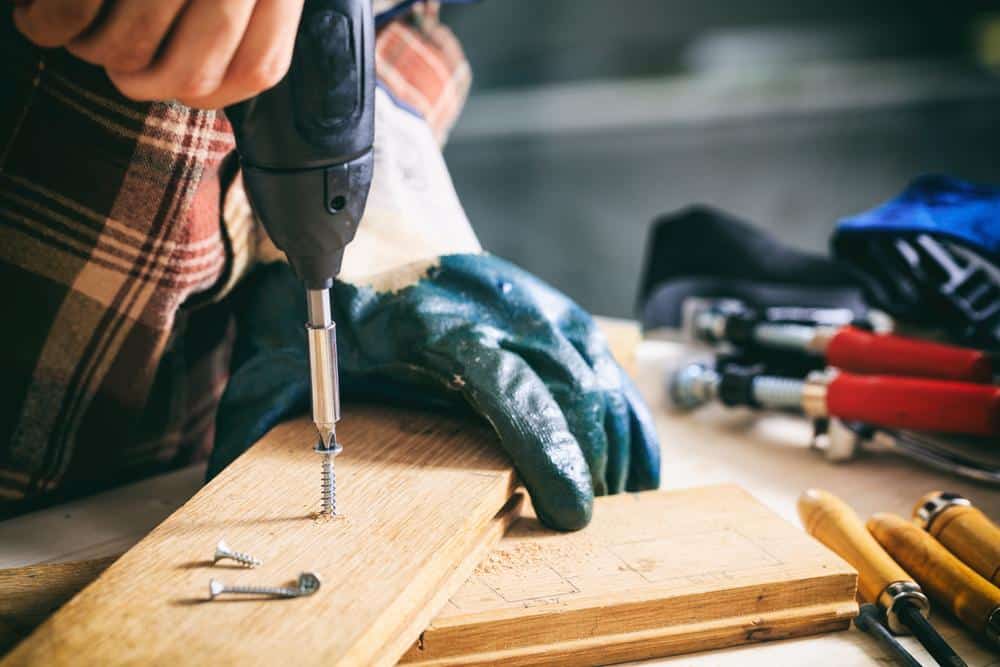
5. Techniques for Using a Cordless Drill as a Screwdriver
To effectively use a cordless drill as a screwdriver, follow these techniques:
I. Choose the Right Bit
Select a screwdriver bit that matches the type of screw you’re using. The most common is the star-shaped Phillips head, for which a No. 2 Phillips head driver bit is suitable. Other bits include an internal hex drive, square drive, and nut setter hex bit, each designed for specific screw types.
II. Adjust the Drill Speed
Set the drill to a low speed when driving screws, especially when using Phillips head bits that may not securely lock into the screw head. Low speed provides better control and reduces the risk of stripping the screw or damaging the work surface. Once you’re comfortable using the drill as a screwdriver, you can increase the speed to expedite the process.
III. Use the Screw Setting
Most cordless drills have a switch with symbols representing a screw, a hammer, and a drill bit. Set it to the screw set to indicate that the drill is ready for screwdriving. The other settings are general drilling and hammer mode for masonry or concrete drilling.
IV. Adjust the Torque Setting
The torque setting determines the turning power of the drill. Use the adjustable collar on the drill to select the appropriate torque setting based on the material and the type of screw you’re working with. Soft materials generally require a low torque setting, while harder materials may require a higher one.
V. Maintain Pressure
When driving screws, maintain a steady pressure on the drill to ensure the bit remains engaged with the screw head. This will prevent slippage and help drive the screw smoothly and securely.
VI. Avoid Overdriving
Be mindful of the torque setting to avoid overdriving on the screw. Overdriving can cause the screw to go too deep into the material or strip the screw head. Test the torque setting at the beginning of the task to find the appropriate level for the job.
VII. Proper Bit Engagement
Ensure the driver bit is properly inserted and seated in the screw head before driving the screw. A worn or damaged bit may not provide a secure fit, increasing the risk of slippage or stripping the screw head.
When it comes to DIY projects or simple household tasks, having the right tools can make all the difference. One such versatile tool is the cordless drill. In our previous article on how to use a drill machine for screws, we explored the fundamentals of using a drill machine for various purposes. Building upon that knowledge, we will now delve into the specific technique of using a cordless drill as a screwdriver. This guide will equip you with the necessary information and step-by-step instructions to efficiently utilize your cordless drill for screwdriving tasks.
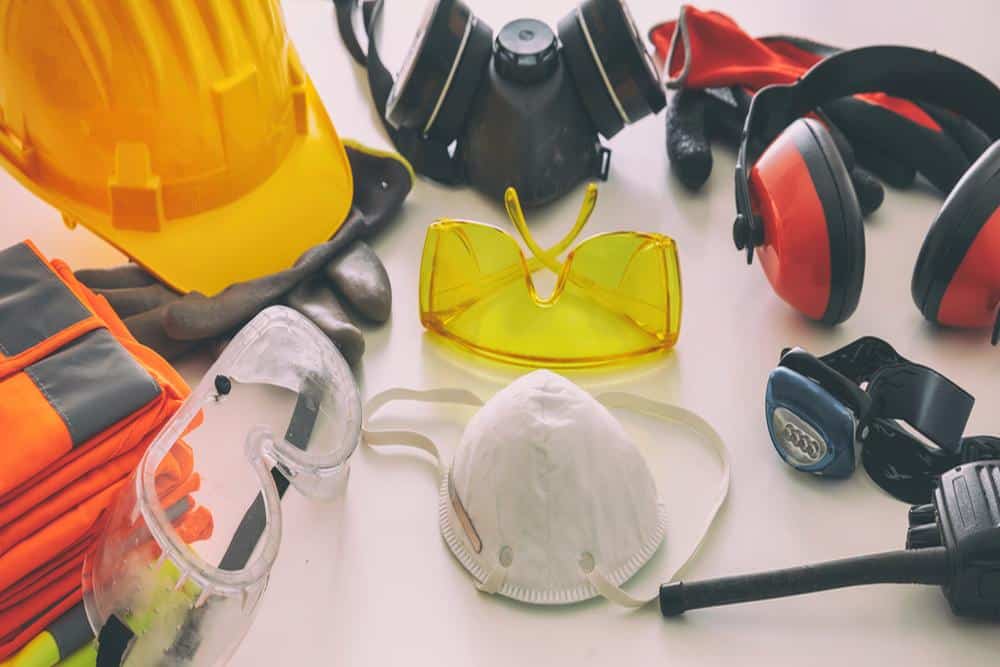
6. Safety Precautions When Using a Cordless Drill as a Screwdriver
While cordless drills are valuable tools, it’s essential to prioritize safety during operation. Here are some important safety precautions to follow:
I. Wear Appropriate Safety Gear
Protect yourself by wearing safety goggles to shield your eyes from flying debris. Use ear protection if the noise level is excessive. If working on projects with the potential for flying particles or debris, wear a dust mask and gloves to protect your respiratory system and hands.
II. Secure Your Workpiece
Ensure your workpiece is securely clamped or held in place before drilling or driving screws. This prevents it from moving or spinning unexpectedly, reducing the risk of accidents and injuries.
III. Keep the Drill and Work Area Clean
Maintain a clean work area, free of clutter and obstructions. Remove any debris or loose objects that could interfere with the drilling process. Regularly clean your cordless drill, especially the chuck, to prevent buildup and ensure optimal performance.
IV. Avoid Over-Tightening
Exercise caution when tightening screws. Over-tightening can lead to stripped screws, damage to the material, or even injury. Use the clutch settings to control the torque applied, and stop tightening once the screw is secure.
V. Store the Drill Properly
Store your cordless drill in a safe and dry place, away from moisture and extreme temperatures when not in use. Keep it out of reach of children and ensure that the battery is disconnected or removed to prevent accidental activation.
Following these safety precautions will help you use your cordless drill as a screwdriver safely and effectively, minimizing the risk of accidents or damage.
7. FAQs(Frequently Asked Questions)
I. Can a cordless drill be used as a screwdriver?
Yes, cordless drills can be used as screwdrivers. They offer the power and torque required to drive screws quickly and efficiently.
II. What is the difference between an electric screwdriver and a drill?
While both tools can drive screws, electric screwdrivers are generally smaller, lighter, and designed specifically for driving screws. Cordless drills, on the other hand, are more versatile, allowing for both drilling and driving functions.
III. What are the benefits of using a cordless drill as a screwdriver?
Using a cordless drill as a screwdriver offers versatility, time and energy savings, portability, flexibility, and increased productivity.
IV. Can a power screwdriver replace a cordless drill?
Power screwdrivers are designed primarily for driving screws and are suitable for lighter tasks. However, cordless drills offer more versatility and power, making them a better choice for drilling and heavy-duty projects.
V. What are some of the best electric screwdrivers available?
Several highly regarded electric screwdrivers exist, including models from popular brands such as Bosch, DEWALT, and Makita. It’s recommended to read reviews and compare features to find the best electric screwdriver.
8. Conclusion
Cordless drills are versatile and indispensable tools for DIY enthusiasts, professionals, and homeowners alike. Their functionality as drills and screwdrivers provides convenience, efficiency, and flexibility. You can make the most of your cordless drill as a screwdriver by understanding the different types of cordless drills, choosing the right tool for your needs, and employing proper techniques and safety precautions. Enjoy the benefits of increased productivity, time-saving, and versatility as you easily tackle various projects.